A Solution, Kaizan: The Power of Small and Regular Improvements
In this issue:
· Insights Into Practices
· Kaizan
· A Poem
· Weekend Workshop at Green Gulch Farm, November 1 – 3
“Don’t stop the line.” For many years this was an agreement, almost an unwritten law of the General Motors assembly lines building cars and trucks. Management believed that keeping the car assembly line going at all times was essential. According to a 30-year GM employee, management assumed that “If the line stopped workers would play cards or goof off.” As a result of this philosophy and way of working, problems were ignored instead of addressed. Defective cars, some missing parts, or cars with parts put on backwards were put into their own special “defective” lot. This lot grew to enormous proportions. Addressing and fixing these problem cars became too costly.
In late 2008, a group of General Motors assembly workers were sent to Fremont, California, as part of a GM/Toyota collaboration called NUMMI. Several GM managers were flown to Japan to learn Kaizan, the Japanese methodology for building cars. What they discovered— was an amazing aha! Anyone on the assembly line who had a concern about the quality of a part could stop the line at any time. Problems were addressed immediately. Groups of workers got together and solved problems. Toyota managers assumed that their workers wanted to build the best cars possible, and though facing problems immediately might have short term negative consequences, it would have enormous long-term benefits. Toyota consistently built better quality cars with more efficiency and lower costs.
General Motors resisted change, went into bankruptcy, and needed to be bailed out in 2008 by American taxpayers for many reasons. There were so many problems facing the company, but one notable contribution to its downfall was producing a poor quality product caused in part by not stopping and solving problems.
It is easy to look at GM and see their folly, and this particular GM tale is a well-known story in today’s organizational effectiveness lore. But what about my company and my life, and your company or your life?
When do we not face “small” problems and put them off till later?
In my coaching and consulting practice, I notice many versions of “don’t stop the line.” It might take the form of:
Don’t question the boss.
We’ve always done it this way.
Don’t confront the rude star salesperson.
We are just too busy right now!
There are many subtle and not so subtle behaviors and habits of overlooking and avoiding problems in the world of work (and outside of work.) Stopping, admitting mistakes, working collaboratively and improving processes that are for the good of the organization, require courage, and the willingness to stop, pause, and ask difficult questions.
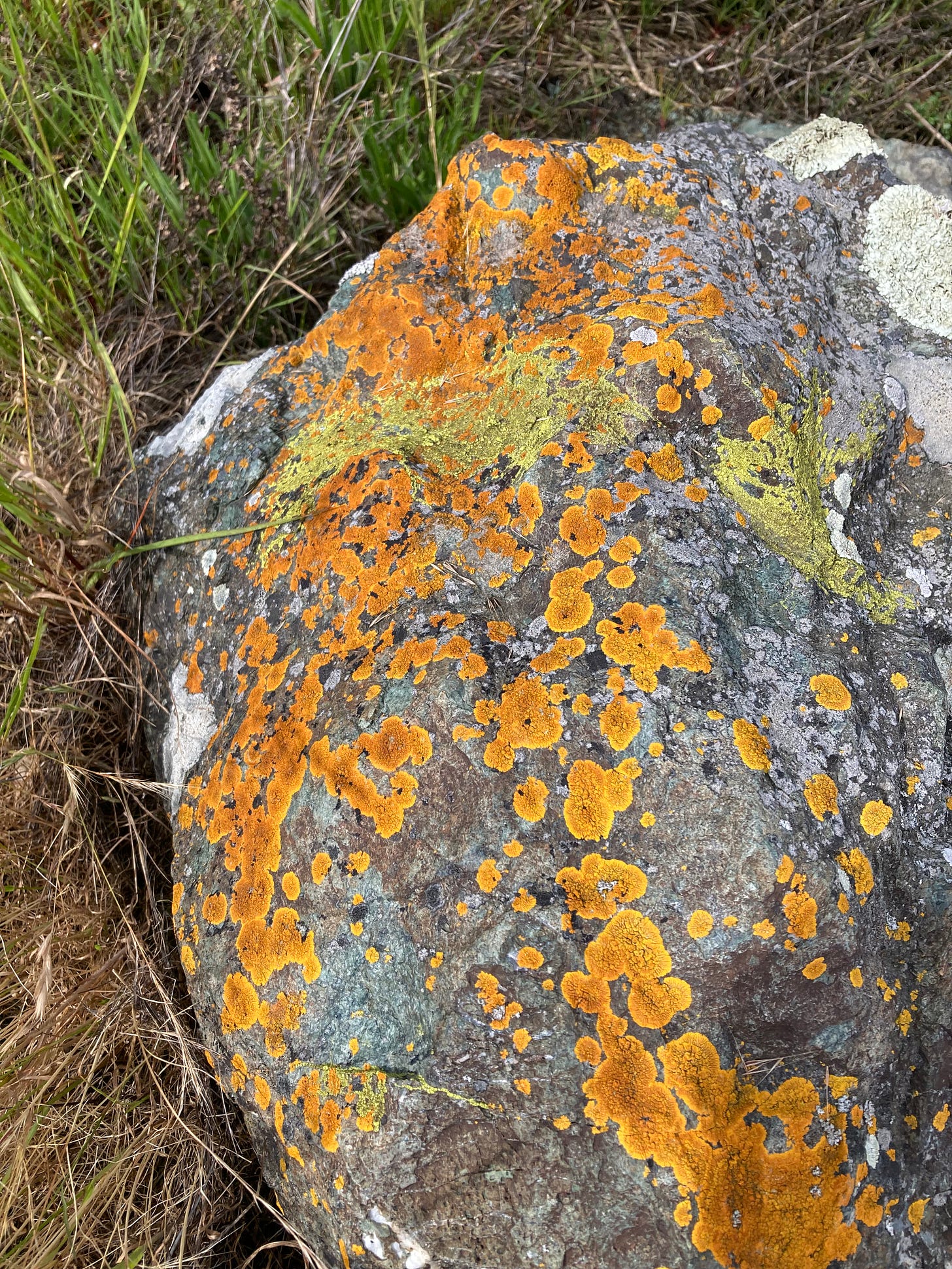
Some questions:
What version of “don’t stop the line” is embedded in your organization, relationships, and your life?
What might stopping look like?
How might your work and life benefit from stopping and pausing? What are the risks? What might the rewards be?
Kaizan
Here are some of the core steps from the Kaizan approach:
1. Identify the problem. Start small.
2. Learn from mistakes:
Figure out what went wrong, learn, and move on.
3. Celebrate small wins:
The small things add up.
4. Value feedback:
Listen to what others say.
Their insights can help you improve.
5. Get others involved:
Teamwork is important and valuable.
7. Reflect on your progress:
Take time to look back at your improvements.
Then, set new goals.
8. Repeat, with patience and possibility:
There’s almost always room for improvement.
Keep looking for ways to learn, grow, and to find solutions.
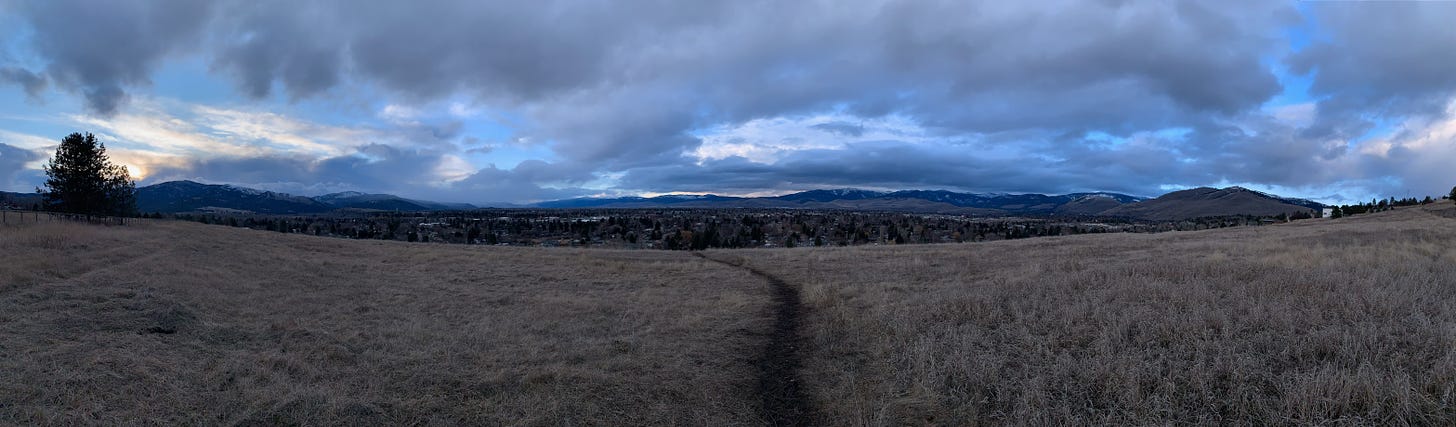
A Poem
Our Story, by William Stafford
Remind me again—together we
trace our strange journey, find
each other, come on laughing.
Some time we’ll cross where life
ends. We’ll both look back
as far as forever, that first day.
I’ll touch you—a new world then.
Stars will move a different way.
We’ll both end. We’ll both begin.
Remind me again.
Step Into Your Life: A Zen Inspired Retreat
November 1 – 3
Green Gulch Farm
In our world of busyness, of more, faster, better, this retreat offers time to stop, reflect, and renew – a time to step fully into the richness of your life. Together we’ll follow a gentle schedule of sitting and walking meditation, interspersed with talks and discussions from the wisdom of Zen teaching as we explore how these stories and dialogues may be utilized in our relationships, our work, and our lives.
We will practice with the essence of meditation, just sitting with what is. And we will experience a variety of guided meditations, exploring our inner voices, our intuition, and our emotions. Through meditations, conversations, awareness practices, and writing we’ll create a safe, vital, and meaningful time of learning together. This retreat is open to all people interested in stopping, exploring, and bringing more awareness and mindfulness to daily life.